Everyone in the AGL world knows that developing an AGL product isn’t simple. It takes a lot of development time, meetings, designs, discussions on the materials to use with the vendors, and of course tests, tests, tests. So what does it take to make sure that whatever product is developed we know that it fully corresponds and often exceeds the FAA requirements?
First of all, we establish a stringent test plan that outlines the FAA requirements and set up a series of tests that will be used by the FAA to test our lights. And, since we are a global brand, we don’t only do FAA testing, but also ICAO (important for Canada and Latin America) and tests to comply with many local governing bodies. This means that when a MULTI ELECTRIC light is launched it has proven to be fully compliant to the FAA requirements and many more.
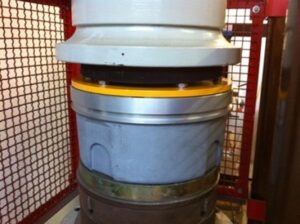
Static Load Testing at MULTI ELECTRIC
The first test is related to photometric testing with ICAO and FAA requirements being different. We need to make sure the photometric output of each light – a key part of the visual guidance principles – corresponds to both requirements. Did you know that ME tests every light that leaves the factory, this is quite exceptional as most vendors do only a sample test?
The next series of tests involve the electronics, testing the electrical characteristics including the electrical discharge, the flickering of the lights, intensity ratio, how the product electronics behave with an arctic kit, LED burn tests, and monitoring tests.
But it doesn’t stop there: we then test how the product behaves under high or extremely low temperatures, corrosion, EMC, vibration, thermal shocks, frangibility.
To test water ingress, lights get tested under water. To test the heat resistance of the light and all components, we put them in a specially designed oven and, for surge tests we organize an overvoltage test, for the EMC test we test on radiation and frangibility, and wind blasts are tested again by another machine. For the entire testing procedure alone, the R&D Validation & Testing lab needs to reserve a lot of space for all the required machinery, but that’s what it takes to be sure that AGL Lights withstand all weather and use conditions.
The test plan takes the R&D Validation & Testing engineers through the different steps of testing that need to be performed, some can be done rather fast while others (the rain test) can take days or even weeks. If all goes well, the full testing cycle takes several weeks before the product is validated at MULTI ELECTRIC.
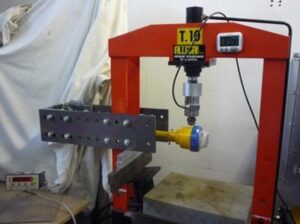
Frangibility Testing at MULTI ELECTRIC
It doesn’t end when all tests have been performed. Several certification bodies need to run the same tests again in their labs. This means that the Quality Process before a product comes to the market is a lengthy one that can take up to two months not counting if a test fails. If so, the product needs to be analyzed and the reason for the failure fully understood and the design eventually updated so the malfunctioning part gets replaced and the overall product goes back in validation testing.
To have a product that belongs to the top range of the AGL world you don’t only need to have the brightest heads united around the product’s development, you also need to have a good understanding of the history of all products and components and… a lot of patience before the product is brought to the market.
But as with every aviation-related product, it’s all about efficiency, sustainability, and above all safety, so no compromises there.
For more information around MULTI ELECTRIC’s products and how they contribute to the safety of ever more airports, contact us at sales@multielectric.com.